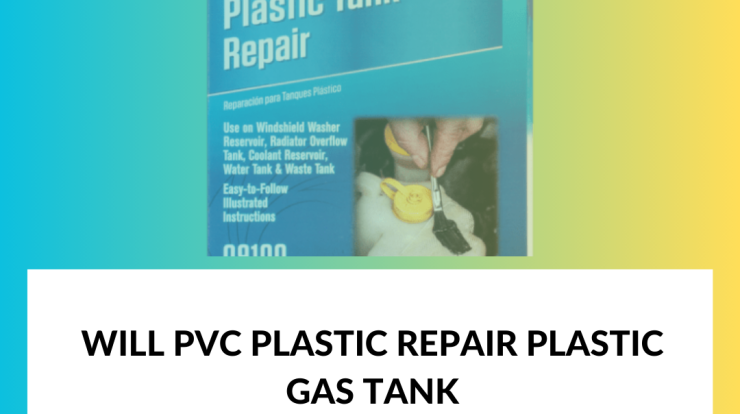
Will pvc plastic repair plastic gas tank – Those who have leaks or cracks in their plastic gas tanks routinely express this worry. Though its adaptability and durability make PVC material valuable in many different uses, its fit for gas tank repairs should be carefully thought out.
Making wise judgments regarding gas tank repair depends on an awareness of the features of PVC plastic, the several types of damage that could arise, and the several repair techniques.
This article explores PVC material and its possible application in repairing damaged gas tanks. We will discuss the advantages and disadvantages of using PVC plastic for this use, weigh it against other often used materials, and clarify the several repair possibilities.
We will also discuss safety issues and provide substitute repair solutions for those seeking something different.
Understanding PVC Plastic and Its Properties
One widely used synthetic material with great flexibility is polyvinyl chloride (PVC). Its attractiveness comes from its unique characteristics that fit a broad spectrum of uses. Finding PVC’s fit for gas tanks depends on knowing its composition and characteristics.
Chemical Composition and Structure of PVC
Vinyl chloride monomers repeated in sequence form the polymer known as PVC. With n the number of repeating units, PVC’s chemical formula is (CH2CHCl)n. The long chain of carbon atoms that makes up PVC consists of chlorine atom attachments.
The properties of PVC owe much to one chlorine atom.
Advantages and Disadvantages of PVC for Gas Tanks, Will pvc plastic repair plastic gas tank
One of PVC’s several benefits for gas tank construction is:* Cost-effectiveness: PVC is a reasonable choice for gas tank construction since it is rather cheap to produce.
Durability
Since PVC can withstand a wide spectrum of temperatures and pressure levels, it is well-known for its strength and longevity.
Corrosion resistance
Perfect for uses involving contact with fuels and chemicals, PVC is quite corrosion resistant.Still, PVC has several drawbacks.PVC is not quite impermeable to gases, hence some fuel vapours can pass through it.
Flammability
Although PVC is said to be self-extinguishing, it can still burn under some circumstances, therefore posing a safety issue.
Environmental concerns
Production and disposal of PVC might affect the surroundings in terms of the release of harmful chemicals.
Comparison of PVC with Other Materials for Gas Tanks
Often used in gas tanks, PVC is often compared to other plastics including polypropylene (PP) and polyethylene (PE).
Types of Damage to Plastic Gas Tanks
Though strong, plastic gas tanks are prone to several kinds of damage. Correct maintenance and repair depend on an awareness of these issues and their causes. This information will enable you to run your car effectively and safely and prevent future damage.
Impact Damage
Particularly in cars involved in accidents or on challenging terrain, impact damage is rather common. Dents, splits, or punctures in the plastic tank can all result from trash, collisions, or just aggressive handling. These damages could lead to fuel leaks, therefore compromising the integrity of the tank and possibly creating safety hazards.
Corrosion
Although plastic is usually corrosion-resistant, several chemicals and environmental factors can nonetheless damage it. Over time, corrosive materials including road salt, acidic fluids, some cleaning chemicals, can break down plastic.
Leaks and fissures resulting from corrosion can compromise the tank’s integrity.
Environmental Factors
Damage can be brought about by extreme temperatures, UV rays, and other environmental factors as well. High temperatures can make plastic fragile and prone to fracture. Plastic can be destroyed by UV radiation, therefore weakening it and increasing its susceptibility to damage.
Examples of Damage Impact
- Fuel Leaks: Fuel leaks resulting from tank cracks or punctures can seriously compromise safety. A leaking tank can also damage surrounding parts including the engine or exhaust system.
- Reduced Fuel Capacity: Dents or deformation in the tank can lower gasoline capacity, which calls for regular refills and may limit the vehicle’s range.
- Vapor Emission: Damaged tanks could let fuel vapors escape, aggravating air pollution and maybe affecting vehicle performance.
Repairing Damaged Plastic Gas Tanks with PVC Plastic: Will Pvc Plastic Repair Plastic Gas Tank
One somewhat cheap and dependable solution is fixing a broken plastic gas tank out of PVC plastic. In plastic gas tanks, PVC plastic—known for its chemical resistance and strength—may effectively fix cracks, holes, and other damage. For tanks that are impossible to replace or no longer under warranty, this approach is rather successful.
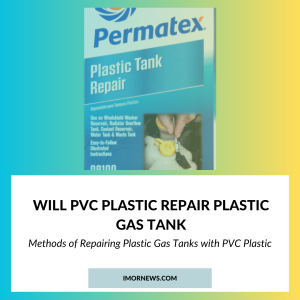
Methods of Repairing Plastic Gas Tanks with PVC Plastic
Repairing a broken plastic gas tank made of PVC plastic calls for a number of steps including cleaning, surface preparation, application of PVC plastic, and curing.
- Cleaning the Damaged Area: Starting with a solvent-based cleaner, completely clean the damaged area to eliminate dirt, trash, and any current coatings. This gives the PVC material great binding power with the tank.
- Preparing the Surface: Sandpaper or a wire brush should be used to rough the surface following cleaning. This offers the PVC plastic a more appropriate surface on which to stick to.
- Applying PVC Plastic: PVC plastic can be applied in the following several ways to the damaged area:
-
- Patching: Repairing minor cracks or holes calls for a properly sized and shaped patch of PVC plastic. The impacted region is then covered in the patch using a strong adhesive.
-
- Welding: Using a PVC welding technique can help you to fix bigger holes or cracks. This means melting the PVC plastic then fusing it to the impacted region with a heat gun.
-
- Bonding: An often used technique for fixing holes in plastic gas tanks and fractures is bonding. The damaged area is filled with two-part epoxy resin, therefore producing a robust and long-lasting bond.
- Curing: Following application of PVC plastic, it needs to be correctly cured. Usually, this means following manufacturer recommendations by letting the glue or weld to totally dry.
Choosing the Right PVC Plastic and Adhesive
The choice of the suitable components determines how well a plastic gas tank made of PVC plastic repairs.
- Type of PVC Plastic: The kind influences the features of PVC material. Selecting a kind appropriate for the gas tank material and resistant to the compounds it will come across is quite vital.
- Adhesive: Strong and long-lasting adhesive is what holds the PVC material to the tank. It should be chemically resistant in addition to suitable with tank material and PVC plastic.
Safety Considerations and Precautions
Fixing a plastic gas tank calls great care since handling combustible materials and even harmful chemicals could have disastrous results. Emphasizing safety all through the restoration process is absolutely important.
Safety Hazards Associated with PVC Plastic and Gas Tanks
Working with gas tanks and PVC plastic puts several safety hazards. These risks come from gasoline’s flammability, fumes and vapors’ potential, and the chemicals used in the repair process.
- Flammable Vapors: Gasoline is quite flammable, hence its fumes can ignite really readily. Working in a poorly ventilated area could produce flammable vapours, therefore increasing the risk of fire and explosion.
- Toxic Fumes: The chemicals and PVC plastic used in the repair process could produce dangerous fumes. Inhaling these fumes could cause dizziness, respiratory issues, and other medical difficulties.
- Fire Hazards: Combining flammable gasoline with possible ignition sources—like sparks from tools or static electricity—may cause a fire.
- Chemical Burns: Some of the components used in PVC plastic repair could irritate skin or eyes or burn.
Importance of Using Appropriate Safety Equipment and Procedures
Follow strict processes and use appropriate safety gear to help to lower these risks.
- Personal Protective Equipment (PPE): Wear the proper PPE, including respirators, gloves, and safety goggles. The respirator should be designed especially for organic fumes, which usually result from solvents and gasoline.
- Ventilation: Work in a well-ventilated area to help to prevent the accumulation of combustible vapors. Use a fan or another ventilation system to keep appropriate air flow when working indoors.
- Fire Extinguisher: Maintaining a fire extinguisher close-by will help you should a fire strike.
- First Aid Kit: Keep a first aid kit on hand should an accident or injury strike.
- Grounding: Ground all tools and equipment to prevent static charge accumulation, which can ignite combustible gasses.
Proper Handling and Disposal of PVC Plastic and Solvents
Proper handling and disposal of PVC plastic and solvents will help to protect the environment and human safety.
- Storage: Store solvents and PVC plastic in well-ventilated areas free of heat and ignition sources. Leave them in their original containers, labels still on.
- Disposal: Dispose solvents and PVC plastic in line with municipal guidelines. Never pour them down the drain or into the surroundings. There are now hazardous waste disposal sites in many towns.
- Cleaning Up Spills: Should a spill arise, immediately clean it with the suitable absorbent materials. Correctly dispose of contaminated goods.
Alternatives to PVC Plastic Repair
Although PVC plastic is a good substitute for rebuilt plastic gas tanks, other materials have clear advantages and drawbacks. Investigating these choices helps you to choose the best fix for your specific situation.
Epoxy Resin Repair
Plastic is among the few materials that Epoxy resin, a strong glue used extensively in attachment and repair, may bind. Perfect for gas tank repairs, it transforms into a strong, waterproof material.
Advantages of Epoxy Resin Repair
- Strong Bond: Epoxy glue creates a strong, long-lasting bond with plastic that will withstand the pressure and shocks of a gas tank, therefore providing a robust repair.
- Waterproof: Epoxy resin keeps the tank’s integrity by being waterproof, so stopping leaks. It is impervious to gasoline tanks’ typical fuels and other chemicals.
- Easy Application: Epoxy resin is delivered in two-part kits that have to be combined before use. Its working time lets one apply it correctly and shape before hardening.
Disadvantages of Epoxy Resin Repair
- Limited Flexibility: Epoxy resin is rigid and may break under stress, particularly in cases of extreme temperature fluctuations or impact on the repair.
- Preparation: Effective epoxy resin repairs depend on correct surface preparation. The damaged region needs to be dry, clean, and free of contaminants if one wants a strong adhesion.
- Curing Time: The stipulated curing time of epoxy resin guarantees its full strength. The type of epoxy and the climatic conditions will affect how long the repair takes.
Fiberglass Repair
Glass fibers woven in a resin matrix make up the composite material known as fiberglass. It is a perfect material for repairing plastic gasoline tanks because of its great strength-to—weight ratio and chemical resistance.
Advantages of Fiberglass Repair
High Strength: Among numerous benefits of fiberglass repair are its great strength and resistance to impact and stress. It generates a long-lasting fix able to withstand the pressures within a gasoline tank.
Flexibility: Because fiberglass is more flexible than epoxy resin, it is less prone to break under pressure or with temperature changes. Repairing areas prone to movement or vibration makes this flexibility rather helpful.
Chemical Resistance: Fiberglass resists many kinds of chemicals, including solvents and gasoline. This guarantees long-term durability and makes this a consistent material for gas tank repairs.
Disadvantages of Fiberglass Repair
Complex Application: Negative aspects of fiberglass repair: intricate application: Layering resin and fiberglass fabric is one of the several techniques used in fiberglass repairs. To offer a solid and long-lasting repair, this operation calls for some knowledge and skill.
Curing Time: Fiberglass resin needs to be cured for a designated period of time if one wants full strength. This can take some time depending on the resin kind and climate.
Weight: Fiberglass gives the rebuilt area weight, which could be problematic for performance cars or applications needing weight loss.