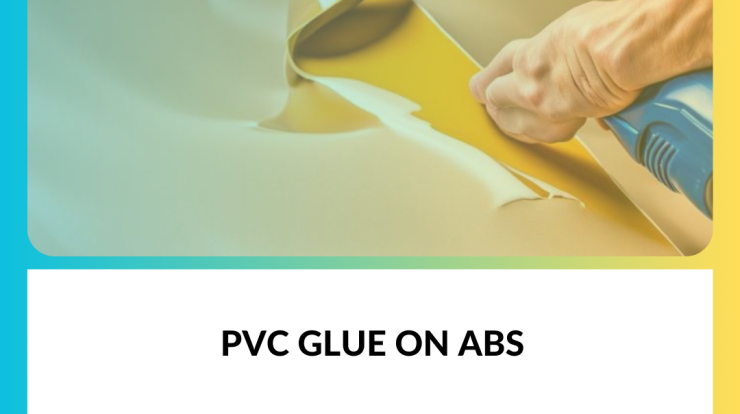
ABS sets the scene for this intriguing narrative by use of PVC adhesive, therefore providing readers with a peek of a creative and detailed beginning story. Flexible adhesive PVC glue excels in adhering ABS plastic, a material known for its strength and general application in many different fields. PVC glue will weld ABS to PVC, but I’m not sure if ABS glue will do the same for PVC.
This mix provides an interesting study of adhesion properties, application techniques, and the several uses of this pairing by PVC adhesive on ABS.
The research looks at the chemical makeup of PVC glue, how it interacts with the unique characteristics of ABS plastic, and the components affecting its successful binding. Emphasizing the need of exact approaches for constructing strong and durable bindings, the story explores the complexity of applying PVC glue to ABS from surface preparation to curing processes.
Introduction to PVC Glue and ABS Plastic
Widely used adhesive to fasten PVC (polyvinyl chloride) plastic is PVC glue, sometimes referred to as polyvinyl chloride glue. Flexible thermoplastic with great impact resistance and durability is ABS plastic, sometimes called as acrylonitrile butadine styree. These materials are often employed in different applications therefore successful bonding depends on an awareness of their properties and compatibility.
Chemical Composition of PVC Glue
Made mostly from polyvinyl chloride (PVC) resin combined in a solvent such as tetrahydrofuran (THF) or methyl ethyl ketone (MEK), PVC glue is essentially a solvent-based adhesive. By acting as carriers for the PVC resin, these solvents enable its surface to permeate and create a strong bond.
Properties of ABS Plastic
Strong, flexible, chemically resistant thermoplastic polymer ABS plastic is known for.
- Strength: Strong impact strength of ABS plastic makes it deformation and breaking resistant. Its great force without breaking makes it perfect for uses requiring longevity.
- Flexibility: Highly flexible ABS material lets it bend and distort without breaking. Applications needing the material to withstand repetitive bending or impact will find its elasticity ideal.
- Chemical Resistance: ABS plastic is chemically resistant, able to withstand solvents, bases, and acids among other compounds. This resistance qualifies for use in places where chemical exposure causes concern.
Common Uses of ABS Plastic
One adaptable material with great utility in many different fields is ABS plastic.
- Consumer Products: Toys, gadgets, appliances, and bags are just a few of the things ABS plastic finds great use in. For these purposes, steel’s strength and impact resistance make it rather good.
- Automotive Industry: Automobile manufacturers use ABS plastic for parts including bumpers, door panels, and dashboards. For these uses, its strength and adaptability are perfect.
- Construction Industry: ABS plastic finds usage in the building industry for pipes, fittings, and other parts. For these uses, its chemical resistance and durability are perfect.
Adhesion Properties of PVC Glue on ABS
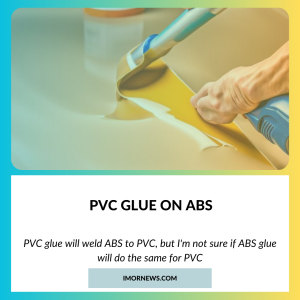
Although ABS plastic can be joined with PVC glue, a common alternative for bonding plastic, the adhesion properties change depending on the situation. This part covers surface preparation, temperature, and humidity as factors affecting the adhesion of PVC adhesive on ABS.
It also contrasts PVC glue’s bonding strength with several adhesives and clarifies the adhesion process between PVC glue and ABS.
Factors Influencing Adhesion
Adherence of PVC adhesive to ABS depends much on surface preparation, temperature, and humidity.
- Surface Preparation: For best adherence, surface pretreatment is absolutely vital. Using a solvent like acetone helps to clean the ABS surface so removing any dirt, grease, or contaminants that can stop adhesion. Sandpaper or a fine-grit abrasive will help to roughening the surface so enhancing surface area and bonding capability. Little flaws created by this process let the glue enter and create a stronger bond.
- Temperature: Adhesion strength of the ABS and its surrounds can be influenced by their temperature. Usually advised is to apply PVC glue room temperature (70°F or 21°C). Higher temperature glue application might hasten drying process while maybe lowering adhesion.
- Humidity: High humidity might cause PVC glue to cure differently, therefore lowering adhesion. Best conditions for PVC glue are dry, low-humidity surroundings.
Mechanism of Adhesion
PVC glue bonds ABS both chemically and mechanically.
Mechanical Bonding: PVC glue forms a mechanical interlock that increases the binding strength by piercing ABS surface flaws.
Chemical Bonding: PVC glue and ABS’s chemical composition lets some degree of chemical bonding possible. The sticky molecules of the glue interact with the ABS molecules to create a link enhancing general adhesion.
Bond Strength Comparison
Generally speaking, PVC glue bonds to ABS with a modest strength. Although it can provide a good connection in many contexts, it could not be as strong as other adhesives as epoxy or cyanoacrylate (superglue).
Epoxy Adhesives: Great strength and long-lasting performance of epoxy adhesives are well-known. Excellent for uses requiring great bond strength, they create a strong chemical link with PVC and ABS.
Cyanoacrylate Adhesives (Superglue): Superglue, a cyanoacrylate adhesive, binds strongly with a range of materials, including ABS and PVC, forming Fast repairs and bonding uses abound for them.
Methods for Applying PVC Glue to ABS
PVC glue has to be correctly prepared and applied to ABS plastic if one wants a strong and long-lasting adherence. Surface preparation, application techniques, and cure times—among the several ways to apply PVC glue to ABS—will be thoroughly covered in this section.
Surface Preparation
Strong binding between PVC glue and ABS plastic depends on appropriate surface preparation. Clean, dry surfaces devoid of contaminants including grease, oil, dirt, and dust should be sought for.
Cleaning: Water and a moderate detergent can help you clean the surfaces. Steer clear of strong chemicals that would compromise the plastic. Clean then gently rinse the surfaces with fresh water and let them dry totally.
Roughening: Roughening the surfaces gently with sandpaper or a sanding block can help to guarantee ideal adhesion. More surface area this offers allows the glue to stick to. For this job, a fine-grit sandpaper ranging in grit between 220 and 400 is perfect.
Application Techniques
Each of the several techniques for adhesing PVC glue on ABS plastic has benefits and drawbacks.
Brushing: Brushing is suitable for little jobs and involves evenly spreading glue using a brush. Although this technique guarantees more perfect application, it takes longer and could lead to uneven glue distribution.
Spraying: Spraying glue is a quicker and more effective method for bigger operations. Both surfaces should get a thin, equal coat of glue applied using a professional glue sprayer. While spraying guarantees consistent application, it also requires enough ventilation and safety precautions.
Dispensing Gun: More exact and controlled application is made possible by using a dispensing gun fitted with a glue cartridge. For applications requiring consistent glue flow, including joining two ABS components, this technique is ideal.
Curing Time and Clamping
It’s important to allow the glue cure properly after application. Temperature, humidity, and adhesive type all affect curing time. For the advised curing time, follow manufacturer instructions.
Clamping or Pressure: Pressing or clamping the bonded surfaces is absolutely crucial throughout the curing process. This ensures correct adhesive sticking and prevents part separation or movement. For the prescribed curing time, keep pressure on the junction using clamps, weights, or another suitable method.
Applications of PVC Glue on ABS
Excellent bonding qualities of PVC glue make it extensively employed in manufacturing, construction, and automotive industries. Its ability to create robust, long-lasting bonds between ABS parts makes it a valuable instrument for many uses.
Applications in DIY Projects
The adaptability of PVC glue reaches to do-it-yourself projects, enabling home enthusiasts and hobbyists to create and fix a range of ABS-based things. Here are few instances:
“For all of my do-it-yourself projects needing ABS plastic, my favorite adhesive is PVC glue. It’s robust, long-lasting, and easy to run.” a satisfied do-it-yourself enthusiast.
Building custom models: ABS plastic model kits including ships, cars, and aircraft can be built with PVC adhesive. It creates a strong, durable link capable of withstanding handling and exhibition’s pressures.
Repairing broken ABS parts: Toys, furniture, and appliances among other ABS components can be repaired using PVC glue. It brings the damaged bits back together so that the object may be once more usable.
Creating unique crafts: Custom jewelry, ornamental items, and personalized gifts are just a few of the imaginative projects where ABS components can be bonded using PVC glue.
Safety Precautions and Considerations: Pvc Glue On Abs
Like any other adhesive, PVC glue needs to be handled carefully to guarantee a successful and safe work. Although it has great bonding qualities, it’s important to know the possible hazards and act to prevent mishaps and health issues.
Proper Ventilation and Protective Gear
One should use PVC glue in a well-ventilated area. Application and drying’s fumes could aggravate the respiratory system, nose, and eyes. Open windows and doors or run a fan to guarantee appropriate airflow. Using a respirator mask fit for organic vapors will aid to guard your respiratory system.
- Avoiding skin contact with PVC adhesive calls for gloves. Select nitrile gloves or other materials resistant to the chemicals in the adhesive.
- Eye protection is absolutely essential. Put on protective goggles or glasses to guard your eyes against splashes and fumes.
- Steer clear of skin and eye contact. Should contact arise, give the affected area at least 15 minutes of thorough water rinsing. See a doctor should the inflammation not go away.
Potential Risks Associated with Using PVC Glue on ABS
The fumes from PVC glue can be harmful and it is flammable. One should be aware of these risks and implement the required protections.
- Stow PVC glue away from heat, sparks, and open flames.
- Apply the glue in a well-ventilated place to prevent breathing fumes.
- Keep PVC glue somewhere cold, dry, well-ventilated away from direct sunlight and heat.
- Use the manufacturer’s instructions exactly for safe handling and storage.
Preventing and Handling Spills or Accidents
There are accidents, hence one should be ready.
- Along with a disposal container, keep a spill cleanup kit on available including absorbent materials like kitty litter or sawdust.
- Should a leak develop, rapidly surround the area to stop the glue from spreading.
- Putty knives or a scraper will help you remove extra adhesive from surfaces.
- Using a wet towel and soap, fully clean any spillage.
- Throw away infected items in line with local guidelines.
Alternatives to PVC Glue for ABS
Although it’s not the only option, PVC glue is a common one used in ABS bonding. Many various adhesives have unique advantages and characteristics that would be more suited for particular uses.Comparatively evaluating their features and stressing their advantages and disadvantages, here is a summary of several substitutes for PVC glue for bonding ABS: :
Epoxy Adhesives
Extreme strength and longevity of epoxy adhesives make them perfect for usage in high-stress environments. They establish a close relationship with ABS since it offers better protection against moisture, heat, and chemicals.There are several forms for epoxies that let for different curing durations, working temperatures, and flexibility.
Their versatility qualifies them for a broad spectrum of projects, from major building to little maintenance.
Advantages of Epoxy Adhesives:
- Stronger Bond: Epoxies are suitable for high-stress uses since they often create a stronger connection with ABS than with PVC glue.
- Higher Heat Resistance: Epoxies fit uses requiring heat protection since they can withstand higher temperatures than PVC glue.
- Greater Chemical Resistance: Epoxies are better chemically resistant than PVC glue, so they are appropriate for uses with solvents or other chemicals.
- Versatile Formulations: There are several forms for epoxies that let one modify operating temperatures, cure times, and flexibility.
Disadvantages of Epoxy Adhesives:
- Longer Curing Time: Epoxies are inappropriate for quick repairs since they often dry more slowly than PVC glue.
- More Difficult to Clean Up: Particularly after drying, epoxy adhesives can be more difficult to clean up than PVC glue.
- Potential for Shrinkage: Some epoxy formulations may shrink when curing, therefore weakening bond strength and producing stress areas.
Cyanoacrylate Adhesives (Super Glue)
Fast-acting and with great adhesion to ABS, cyanoacrylate adhesives—also known as super glue—have When time and convenience count, they are ideal for minor repairs and small bonding projects.
Advantages of Cyanoacrylate Adhesives:
Fast Curing Time: Cyanoacrylate adhesives are ideal for small repairs and bonding projects since they cure fast.
High Bond Strength: Cyanoacrylate adhesives may create strong bonds with ABS, therefore resisting impact and stress.
Easy to Use: Simple to apply and requiring little preparation, cyanoacrylate adhesives are
Disadvantages of Cyanoacrylate Adhesives:
Low Heat Resistance: Reduced heat resistance: Cyanoacrylate adhesives breakdown or fail at higher temperatures.
Limited Chemical Resistance: Some substances have limited chemical resistance, hence they can break cyanoacrylate adhesive connections.
Brittle Bond: Brittle bonding created by cyanoacrylate adhesives make them inappropriate for use under great stress.
Solvent-Based Adhesives
Strong mechanical bond is produced by solvent-based adhesives meant to dissolve the surfaces of the materials being bound. ABS is routinely joined with these adhesives, however they lack the strength of epoxy adhesives.
Advantages of Solvent-Based Adhesives:
Strong Bond: Excellent resilience to stress and shock, strong bond formed by solvent-based adhesives can help ABS
Fast Curing Time: Fast curing times of solvent-based adhesives make them perfect for rapid repairs.
Easy to Use: Often easy to use and requiring minimal preparation, solvent-based adhesives
Disadvantages of Solvent-Based Adhesives:
Low Heat Resistance: Low heat resistance refers to Solvent-based adhesives breakdown or fail at higher temperatures.
Limited Chemical Resistance: Some compounds can compromise solvent-based adhesive bonding by limited chemical resistance.
Potential for Fumes: Solvent-based adhesives can produce harmful fumes, so enough ventilation is needed.